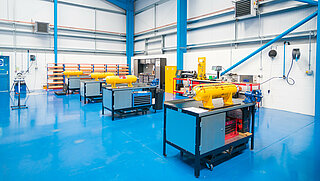
Learn more about our capabilities
QHP has established a global leadership position in the design and manufacture of Hydraulic Accumulators and Compensators for the Oil and Gas market and Petrochemical industry. To support this enviable position we have developed the following processes which are carried out entirely in-house.
Research and Development
As a specialist manufacturer of Accumulators for the Oil & Gas industry, Accumulator qualification testing has always been at the forefront of QHP’s Accumulator research and development.
Using our in-house purpose-built qualification chamber, Accumulator research and development is supported by two dedicated HPU’s. QHP have carried out many Accumulator research projects including customer specific Product Life Simulations.
The Accumulator qualification testing chamber is environmentally approved by Bureau Veritas.
QHP’s Accumulator development and Accumulator research programme has developed a range of Accumulators and Compensators which have undergone full Accumulator qualification testing here at QHP. Many QHP Accumulators have been qualified for a Subsea life of 30 years.
We have the capability to qualify products within the following parameters:
- -40 to +200 Degrees C.
- Up to 2000 Bar.
- Accumulator qualification testing and Accumulator research at QHP can be monitored and recorded 24 hours, 7 days a week.
- Fully comprehensive computerised data – tracking every cycle and every second of the Accumulator qualification testing process.
- Fluids include HW443, Transaqua HT, Transaqua HT2, Brayco, Synthetic Sea Water, Dielectric Fluid and Mineral Oil.
Flushing
Accumulator flushing, Accumulator cleanliness and fluid analysis is carried out at QHP using dedicated Accumulator flushing rigs and laser particle counters. Using dedicated Accumulator flushing equipment allows for the highest levels of Accumulator cleanliness, and eliminates cross contamination from differing fluid types such as water glycols, mineral based fluids and synthetic fluids.
Particle counting is carried out using laser-based fluid analysers. The system analyses bottle samples taken directly from the accumulator flushing process, to confirm the accumulator cleanliness levels and verify that the fluid conforms to specific customer requirements Accumulator cleanliness can be verified to suit NAS 1638, SAE AS 4059 and ISO 4406.
QHP have several Accumulator flushing rigs, as standard we can flush with the following popular fluids:
- Castrol Transaqua HT.
- Castrol Transaqua HT2.
- Mineral Oil.
- Castrol Brayco Micronic SV/3.
- Macdermid Oceanic HW443.
We also have dedicated flushing rigs for small Accumulators and Subsea Compensators.
Whenever Accumulator flushing is requested by a customer QHP will supply a full Accumulator cleanliness report. QHP supply a full documentation package with each Accumulator.
Pressure Testing
QHP have eight dedicated testing rigs for pressure vessel testing. QHP have the capacity to conduct hydrostatic and hydro-pneumatic pressure vessel testing. Within the QHP facility, there are three purpose-built test rooms which are monitored by CCTV cameras to monitor the pressure vessel testing taking place. Testing up to 50,000 Psi (3448 Bar) is possible in-house.
Hydrostatic pressure vessel testing is undertaken in accordance with all applicable Accumulator design standards.
Hydrostatic pressure vessel testing is a process of verifying the integrity of the Accumulator’s pressure retaining envelope to confirm that the product meets the highest standard of safety.
Inspection / PMI
QHP has a ISO 9001:2015 certified quality management system, which is also certified by Lloyds Register.
Every pressure retaining component is inspected / tested throughout various stages of manufacture in order to verify conformance to drawings and specifications, records are kept to confirm conformance of the product inspected.
QHP use portable coordinate measuring machines (CMM) to validate dimensions with a possible accuracy of 0.005mm, this is highly effective in confirming the dimensional quality of precision machined components used in pressure vessels.
As part of QHP’s inspection process, 100% of Stainless-Steel pressure retaining components are subject to positive material inspection (PMI) in order to verify the material grade conforms with customers purchase order.
QHP can offer ferrite testing as an additional service if requested.
CNC Machining
QHP have over 30 years’ experience in large CNC turning, milling and drilling with the capability to manufacture Bladder Accumulators, Piston Accumulators and Subsea Compensator components, in a variety of materials, specifications and tight tolerances.
The quality of machining is in line with ISO 9001:2015 which means QHP have a consistent high-quality volume of work; and have the ability to produce anything from one off prototypes to large volume machining.
Since the acquisition of Alton Precision Engineering in 2017, QHP has invested in seven brand new Doosan machining centres which has increased the output of Bladder Accumulators, Piston Accumulators and Subsea Compensators by 300%.
Fabrication
To ensure a high standard of quality, here at QHP we can offer high quality Stainless-Steel Accumulators and their matching accessories for all requirements in the Offshore, Subsea and petrochemical Accumulator sectors.
Six ASME 1X and EN ISO 9606 qualified welders work in our ISO 3834-2 certified welding facility.
Every Stainless-Steel Accumulator is subjected to a 100% X-ray test and a 100% dye penetrant test. On request, we will be happy to carry out additional, supplementary weld seam tests and quality inspections for you. Likewise, we can also advise you on the choice of material and find the right solution for your project.
Our Stainless-Steel Accumulators have the following characteristics:
- 316 Stainless-Steel Accumulators up to a wall thickness of 27 mm (suitable for offshore Accumulators, underwater storage tanks and petrochemical Accumulators).
- Duplex Stainless-Steel Accumulators" up to a wall thickness of 28 mm (suitable for Offshore, Subsea and petrochemical storage applications).
- Super Duplex Stainless-Steel Accumulators' up to 16 mm wall thickness (suitable for Offshore, Subsea and petrochemical storage applications).
- 254 SMO Stainless-Steel Accumulators up to 16 mm wall thickness (suitable for Offshore, Subsea and petrochemical storage applications).
- Accessories for the Stainless-Steel Accumulator: Accumulator frames, Clamps and Brackets.
Painting
QHP carry out surface preparation and accumulator painting in-house for bespoke customer and QHP standard specifications. QHP have a separate on-site Oil and Gas painting facility, designed specifically for the painting of Accumulators and Compensators.
Approved and qualified Accumulator painting specifications include NORSOK M501 systems 1, 6 and system 7 with the capability of meeting many other international Oil and Gas external coating standards for Accumulator painting. QHP also has two NACE Certified Level 3 Coating Inspectors in-house as well to oversee the applications of Oil and Gas painting, as well as NACE 2 and NACE 1 qualified personnel.
QHP’s Accumulator painting services have been approved by many customers and industries who recognise painting standards for Accumulators. This includes Oil and Gas external coating for Subsea Accumulators, Topside Accumulators and Petrochemical Accumulators.
Currently QHP’s equipment includes:
- Two purpose-built blast rooms (alumina and chilled cast iron) for Accumulator painting.
- Three operational enclosed LEV paint booths - suitable for external coating of Subsea, surface and petrochemical Accumulators.
- Airless spray booths suitable for external coating of Subsea, surface and petrochemical Accumulators.
- Drying rooms suitable for external coating of underwater, surface and petrochemical Accumulators.
- Interlinking rail systems for external coating of Subsea, surface and petrochemical Accumulators.
- All relevant inspection equipment for Accumulator painting is calibrated to traceable national and international standards for oil and gas painting.
During 2023, QHP has invested in excess of £250k into this dedicated Accumulator painting facility, to further develop our resources and ensure that QHP delivers the best quality Oil and Gas external coating possible.
Approvals
- ASME ‘U’ Stamp.
- PED 2014/68/EU – Including modules H and H1 Category IV.
- Det Norske Veritas (DNV) – QHP has a MSA agreement which allows quality control to be kept in-house.
- American Bureau of Shipping (ABS).
- Lloyds Register.
- Malaysian DOSH.
- Canadian CSA- All Provence’s.
- Australian Worksafe.
- Brazilian Certification.
- ATEX 2014/34/EU.
- Chinese SELO.